Recently, we received a request from a nickel processing plant in Central Asia to create large-capacity industrial cooling water pumps. We fulfilled this challenging job order by sourcing rare components and modifying them at our facility.
Cooling water pumps for nickel extraction
The world economy depends heavily on nickel. Without nickel, there would be no stainless steel, rechargeable batteries, special metal surfaces, pigments or numerous other niche products.
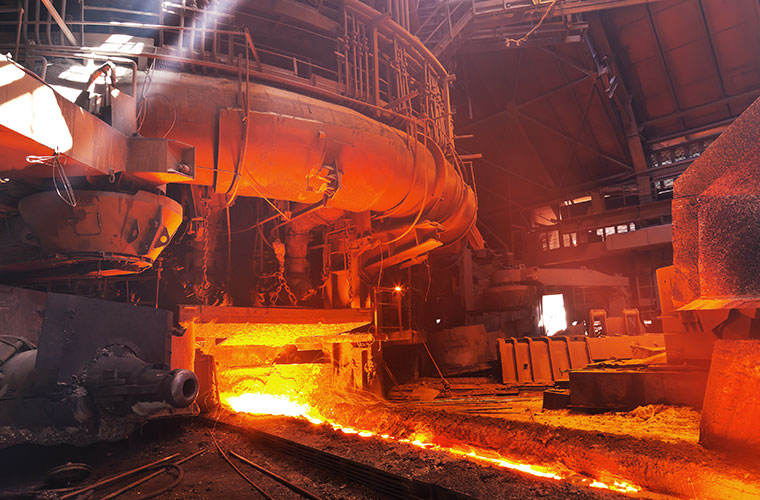
However, extracting nickel from ore requires extremely high and difficult smelting conditions (often reaching temperatures as high as 1,600° Celsius). Nickel processing facilities require extensive cooling block systems for their furnaces. These cooling systems rely heavily on industrial cooling water pumps that are customised according to a particular plant’s specific conditions. Thus, the world relies on these nickel-processing cooling pumps as well.
Our pump engineering team has spent years developing the skills and resources to custom-build cooling water pumps (CWPs) for nickel furnaces of every size. Few pump engineering companies specialise in this. Not surprisingly, clients from all over Australia and other countries often call on us for help.
Overseas nickel processing plant cooling system
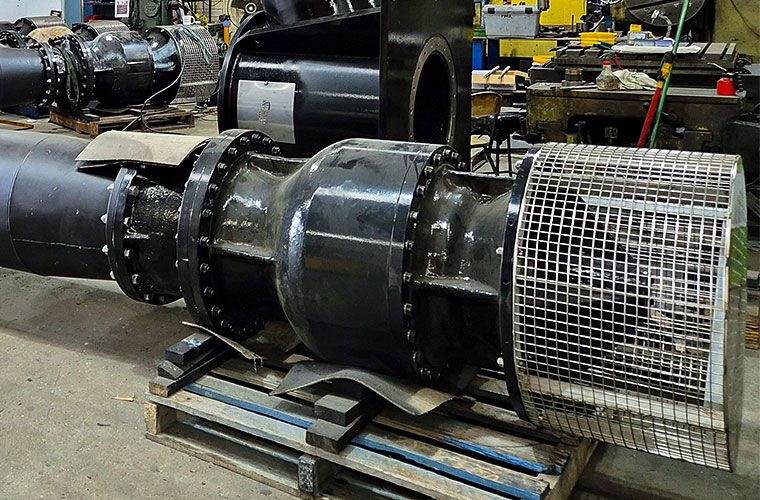
Given our expertise, we were approached to design and build a set of very high-capacity water cooling pumps for the nickel smelting company mentioned above.
The client needed four big vertical cooling water pumps. When in operation, each pump had to be capable of handling high pressures and a massive flow rate of 540 litres of freshwater per second. Each one would be powered by a 400-kilowatt motor. And because the pumped liquid would be either groundwater or river freshwater, any debris that could occasionally flow in had to be filtered out. At this extremely high flow rate, we needed to design components that could withstand any potential impurities as much as possible. It also meant we needed a very high-quality strainer that would last.
Clearly, any heavy-duty pump needs to last for years and requires minimal maintenance. This was especially true for this project, being a remote site with a high flow rate requirement. Our team ensured that the design would not only conform to the client’s specifications but also be long-lasting and readily maintainable.
Meticulous sourcing and custom-fitting
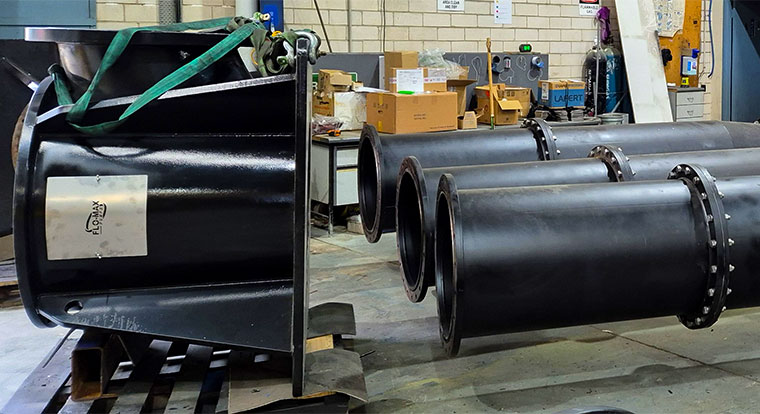
Our first step after design and modelling was to source the most critical components. Our network of partners extends beyond Australia and we have trusted manufacturers in the EU, United States, and Asia who can provide us with massive heavy-duty pipes and pump parts.
For this job order, we chose components that followed advanced pump engineering designs and were made of cast iron. It is critical to ensure heavy-duty pumps are composed of this material, for maximum durability.
Details of the build
From start to finish, the entire custom build took us several months. The process involved designing modifications or additional components, 3D printing, sand casting, refitting and testing.
We also measured, documented and electronically scanned every part of the pump’s components. Having these measurements securely stored in our data records means we can rapidly create any replacement parts as needed by our client in the future.
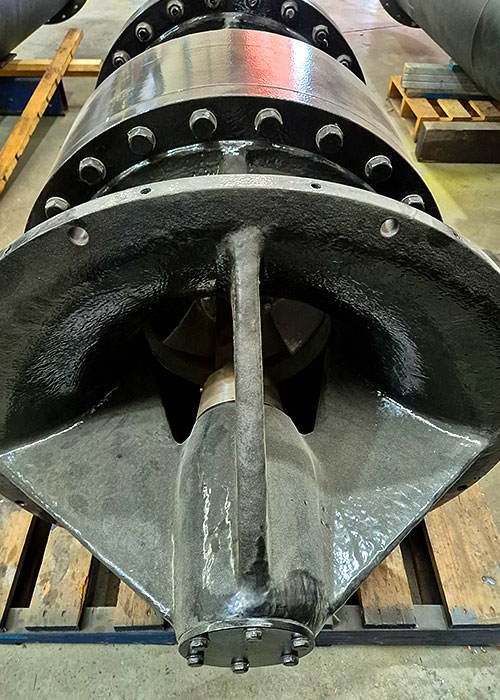
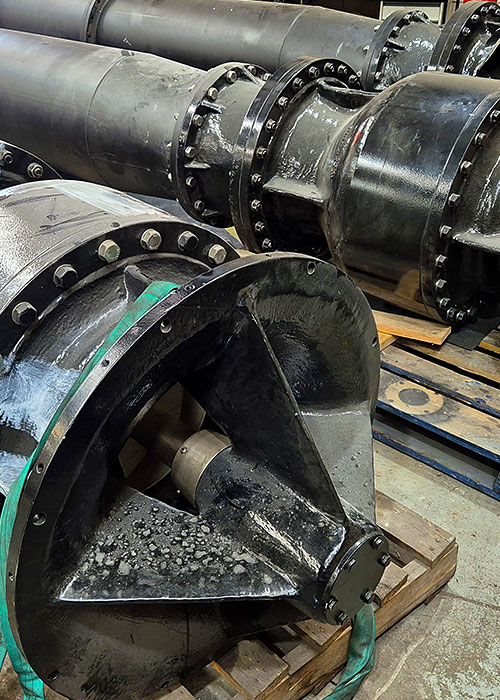
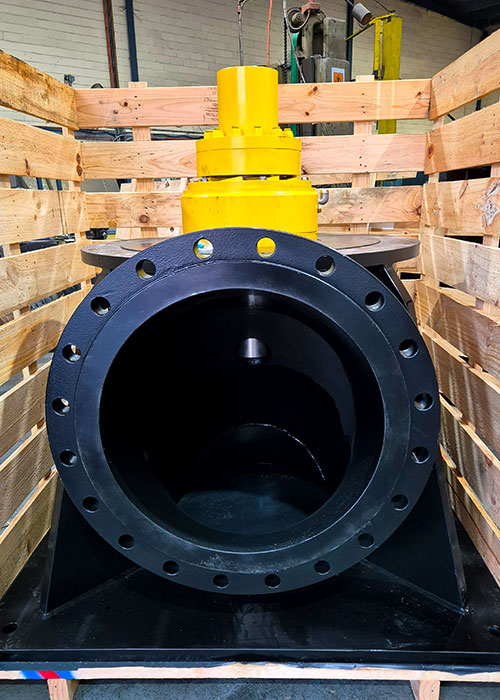

We tested each pump to prove they were up to safety standards before preparing them for shipment. Then we shipped the finished CWPs to Central Asia in partially assembled sections, for easier transport. The smelting company’s engineers will facilitate the full installation and testing at the final location with our guidance.
Pump engineering customisations you can depend on
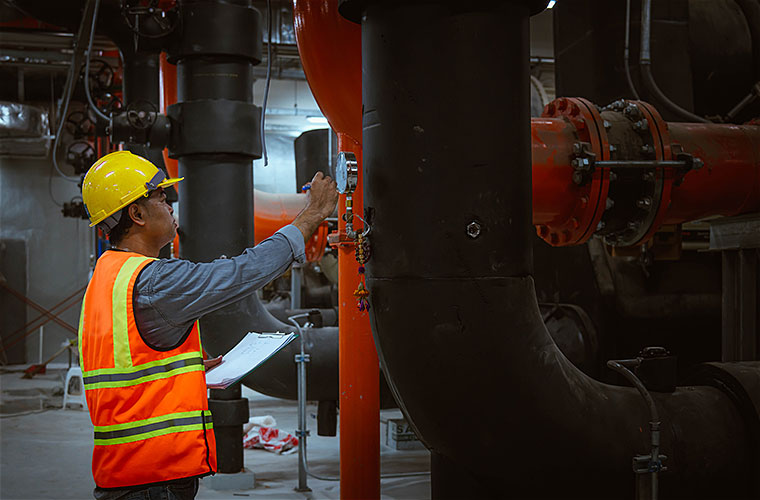
As pump engineers, we’re all about custom designs. From design to sourcing, customising and manufacture, we can help you solve your exact pumping requirements.
By partnering with us, you are dealing with engineers, not salespeople. Deal with the team that has the right track record and knowledge to design customised pumps that meet your specific needs and standards. Like with our Central Asian client here, our goal is to create the right solution for the long term.
Feel free to contact our engineering team today.