Building pumps for specific or extreme conditions requires years of familiarity with that application. This was especially true for a brine axial flow pump we built for an Australian sea salt production site.
Pump engineering for large-scale sea salt production
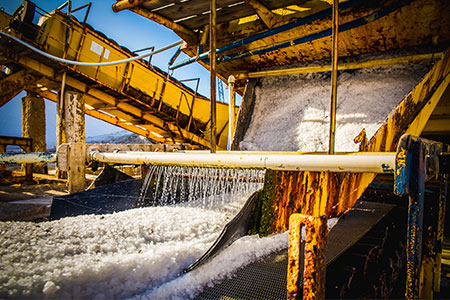
Salt underpins much of our global economy. About 80% of the world’s salt is used in a wide range of industrial manufacturing applications. That includes any process that involves caustic soda, soda ash, chlorine or other products where salt is a key component.
Salt is either mined from natural underground salt deposits (i.e., halite in sedimentary rock) or extracted from seawater. Countries with many seaside bays and coastlines such as Australia typically resort to sea salt extraction.
To meet global demand, large modern sea salt harvesting sites (like those in Australia) produce anywhere from 1 to 2 million tons of salt per year. While the extraction process is essentially the same as in ancient times, the massive production scale requires full mechanisation or automation for maximum efficiency.
Pumps are a critical part of this mechanisation. Large amounts of seawater and brine must be diverted into outdoor evaporation pools and ‘crystallisers’ or salt flats. Once it settles in these pools and flats, the sun naturally evaporates water. The process leaves behind raw salt, which is harvested and processed. After the salt is washed and refined, it is stockpiled and loaded onto special cargo ships for distribution in local and foreign markets.
However, these are difficult operating conditions for machines. Saltwater or brine corrodes most materials, including metals or metal alloys and polymers or plastics. Every pump, vehicle or piece of machinery involved must be serviced or changed every few years.
That poses an ever-present challenge for managers and engineers. They must keep the salt production running smoothly while keeping operating expenses within their budget.
The client brief: a brine-ready axial flow pump
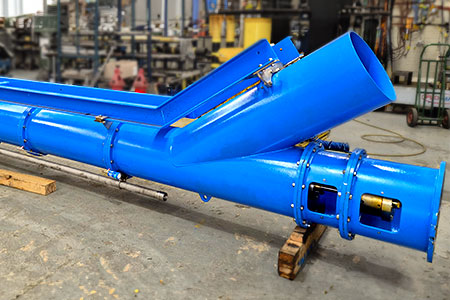
This was the challenge we faced when an Australian ‘solar salt’ producer asked us to design and build this type of pump for them. We had created other pumps for them in the past, so they already knew we could do the job.
For this particular project, they needed an all-weather propeller or axial flow pump to help move condensed sea water or brine across their outdoor condenser ponds. Their maximum pump operating duties usually reach around 400 litres of brine per second.
Moreover, this pump needed to strain out any mud or light debris from the brine as it flowed from one pool to the next. It had to be durable enough to survive or stall corrosion of its components for a few years of operation. While cumulative damage from salt is inevitable, the pump’s build also had to be as low-cost as possible. Future repairs or replacements must be cost-effective in the long run.
Building a durable brine pump at a lower cost
Fortunately, we have experience in building pumps for salt production. For this application, we mainly use regular steel components coated with the appropriate epoxy paint.
This approach yields an axial flow pump that is cost-effective and durable enough to handle brine for a few years. Using more expensive materials does not significantly extend its operating life and will only add extra cost to the build.
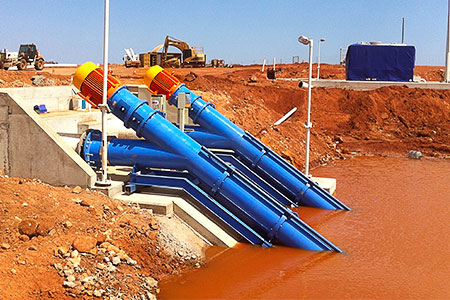
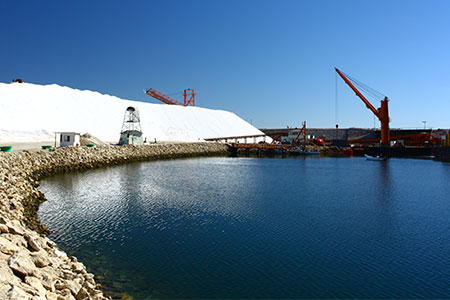
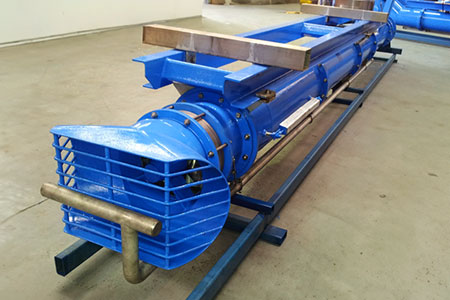
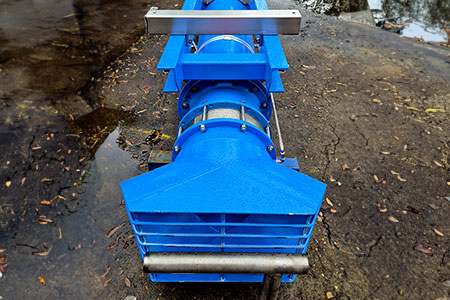
We also keep meticulous records of each pump we build. Thus, this client can reach out to us again for overhauls or additional brine pump orders whenever they need them.
Engineering expertise you can grow your business with
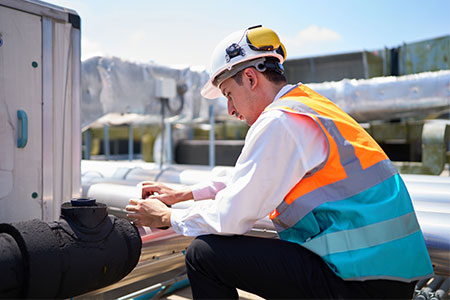
We understand the challenges you face in heavy industries. Your business relies greatly on pump machinery for growth.
Dealing with us means dealing with pump engineers, not pump salespeople. We’ve spent years amassing expertise in designing and creating pumps for various industries that operate in highly specific or difficult conditions.
Discover how our knowledge of industrial pumps can help keep your business operations efficient and profitable. Contact our team today and we’ll find the best pump engineering solutions for you.